About Toroidal Transformers
These are power transformers utilizing a toroidal core. Primary and secondary coils are wound on this core and the toroidal shape allows for a shorter mean length per turn, reducing I2R losses in winding which are the main losses in this type of transformer yielding a smaller design improving overall efficiency.
Line frequency toroidal transformers start with a core made from a continuous strip of thin, typically M4, grain-oriented electrical grade silicon steel. Silicon grains in the steel are oriented based on the rolling direction of the steel and is slit parallel to that orientation, creating the preferred path for magnetic flux. Strips are available in numerous widths; for smaller and mid-sized cores these are typically available in 1mm increments, and larger toroidal cores strips are available in 5mm increments.This steel has a thin inorganic coating for high interlaminar resistance, providing insulation between lamination windings and a good stacking factor.
To create the core, a strip of grain-oriented electrical grade silicon steel is tightly wound under controlled conditions and tension on a mandrel, similar to a clock spring with the ends spot-welded in place, assuring a firm and congruous magnetic path. Unfortunately winding of the core creates mechanical and magnetic stresses, which change the molecular structure of the core. To return the material to a fully stress relief condition, the core is placed in an annealing furnace. Using a precise heating and cooling profile ensures that the silicon grains are in the single preferred magnetic direction.
Core insulation consists of four layers of 2mil polyester film (other materials are available) applied to the core using a toroidal tape winding machine. This insulation provides 100% surface coverage, also protecting and cushioning the core from the windings and reducing vibration. Primary windings are applied by a toroidal winder and if needed lead wires are attached. The primary to secondary insulation uses the same process and materials as the core insulation, to meet standard test requirement of 4kV RMS for 1 minute between primary and secondary.
Secondary windings are applied by a toroidal winder and if needed lead wires are attached. The copper wire has a base coat of polyester and heavy topcoat of an amide imide (200°C). The copper wire is wound uniformly over the entire core to provide: better heat dissipation, minimum flux leakage, and to maintain a low voltage between adjacent turns. The outer insulation is then applied using the same process and materials as the other insulation layers, except only two layers of polyester film are used.
Toroidal Transformer Design Options
- Thermal Protection - Usually in primary circuit, normally closed-auto reset opens at high temperature UL, CSA, VDE listed components.
- Center Hole Potting - Thermoplastic material for high mounting precision. Threaded insert or press fitted stud is optional. Thermally conductive compound is available.
- Electrostatic Screen - Copper foil (2mil) laminated between polyester film and tape to reduce capacitive coupling between primary and secondary windings, tightly wound over primary insulation.
- Medical / Safety Shield - Polyester laminated (5mil) copper foil creates a physical barrier between primary and secondary windings, terminated at one end with green and yellow earth wire to meet UL2601 and IEC601.
- Magnetic Shield - Several turns of silicon grain-oriented silicon steel are tightly wound around the toroidal circumference, fixed in place by outer insulation.
Toroid Mounting Options
Toroid Mounting - Disk | Toroid Mounting - Flange | Toroid Mounting - PCB
Toroid Metal Disk Mounting Exploded View

50/60Hz power toroidal transformers have unmatched flexibility and efficiency providing a higher performance compact transformer. Since there is no air gap, it results in a stacking factor of 97.5% of its weight. Power toroidal transformers can also operate at higher flux densities than E-I transformers, thus reducing the number of turns necessary to induce a given voltage across the same cross section of the core. This means a lower series resistance in the winding, reducing the I2R copper losses. Given the same power output requirements, ambient temperature, and temperature rise allowances, a toroidal transformer will use less material to produce an equivalent transformer leading to a smaller and lighter solution than an equivalent E-I laminated transformer. With all the above reasons the question should not be “Why choose a toroidal transformer,” it should be why not!
Toroidal Transformer Core Compared to EI Core
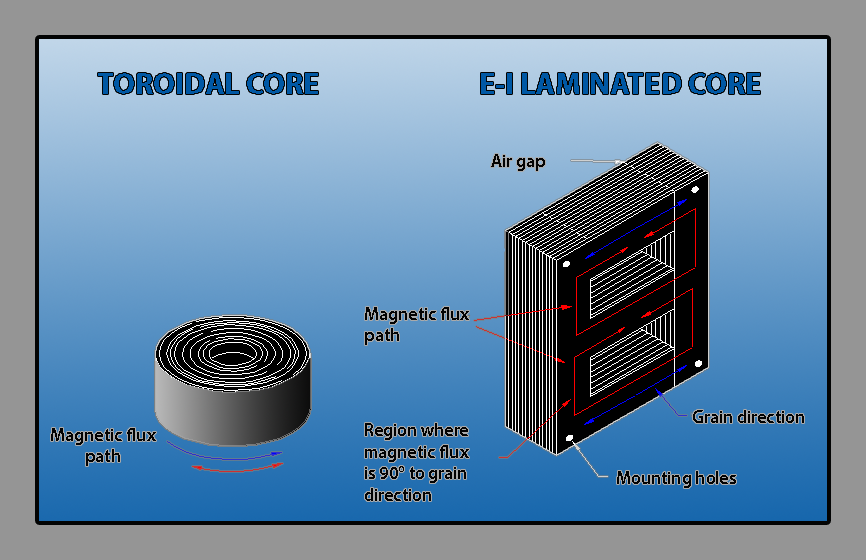
SIMPLIFIED MOUNTING
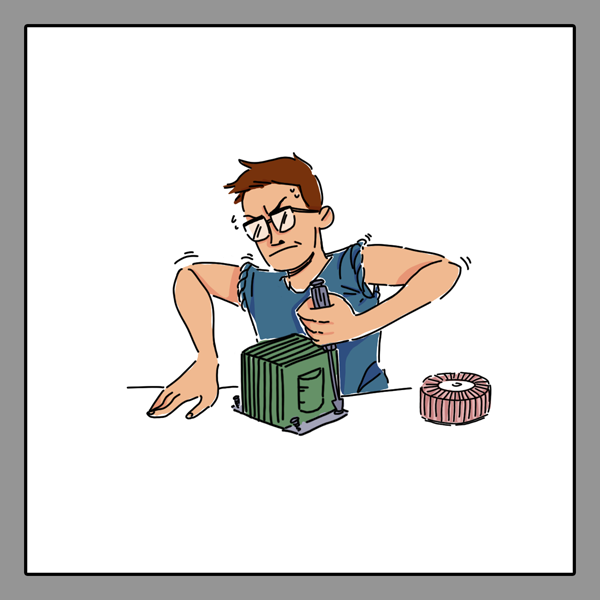
A one bolt mounting scheme easily and quickly mounts the toroid, avoiding costly mechanical design and tooling charges associated with the first piece of custom conventional E-I laminated transformers. A power toroid, toroidal auto transformers and toroidal medical grade isolation transformers have a low center-of-gravity along with reduced weight, such that a lower gauge sheet metal is required to support a toroidal transformer. This, further reduces your product’s weight and material and labor cost by eliminating three screws per assembly.
LOW NO-LOAD LOSSES
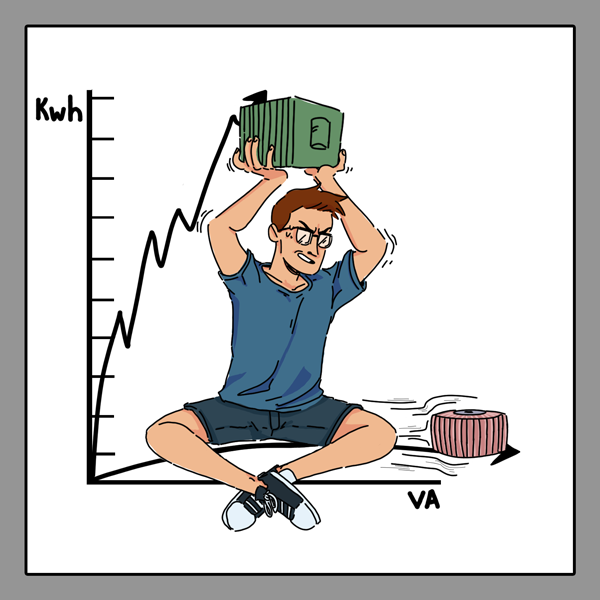
Compared to conventional E-I transformers, toroidal power transformers have extremely low no-load losses. When used in an application where a circuit is in a quiescent or “stand-by” mode for long periods of time, the potential power reduction can be significant, sometimes 80% to 90% lower.
LOW WEIGHT
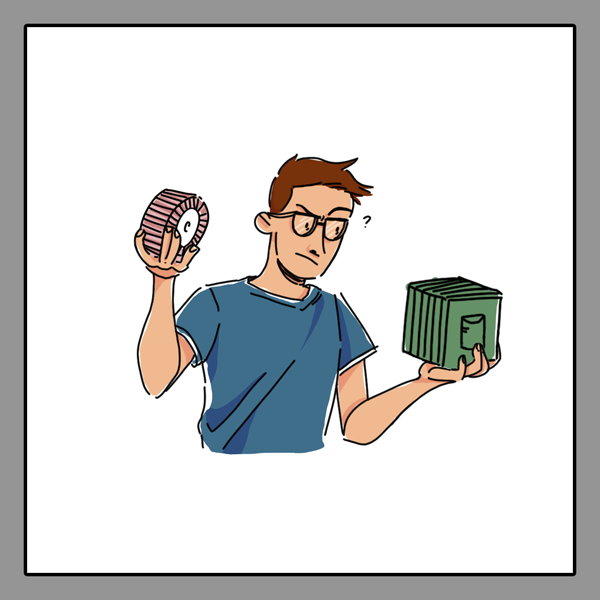
Because they are more efficient, toroid isolation transformers and toroidal auto transformers can be up to 50% lighter (depending on power rating) than E-I laminated transformers. Low weight simplifies end product design by reducing mounting hardware and supporting enclosure requirements.
LOW ACOUSTICAL NOISE
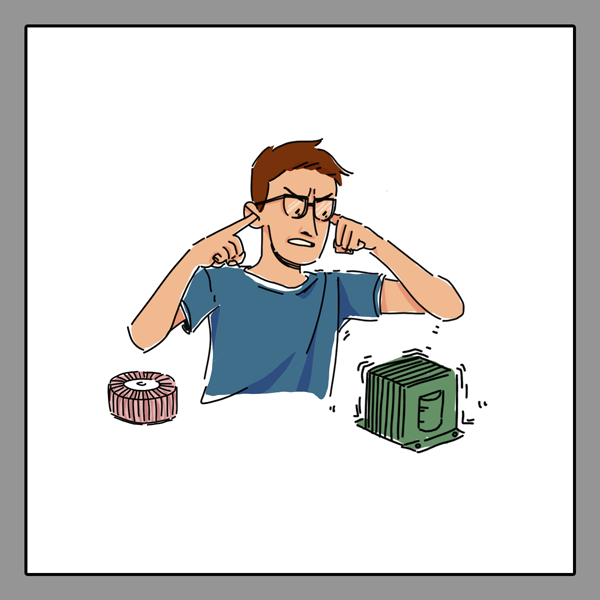
The core of a toroid transformer is formed from a single strip of grain-oriented electrical grade silicon steel, tightly wound in the form of a clock spring with the ends spot-welded in place. The copper wire is wound over polyester film, forming a silent, stable design without the use of environmentally harmful glues or varnishes. It will not clack or buzz anywhere near the level as would many pieces of separate lamination under the same changing magnetic field. The core actually intensifies the field, not contributing to the problem of layer-to-layer vibration.
HIGHER EFFICIENCY
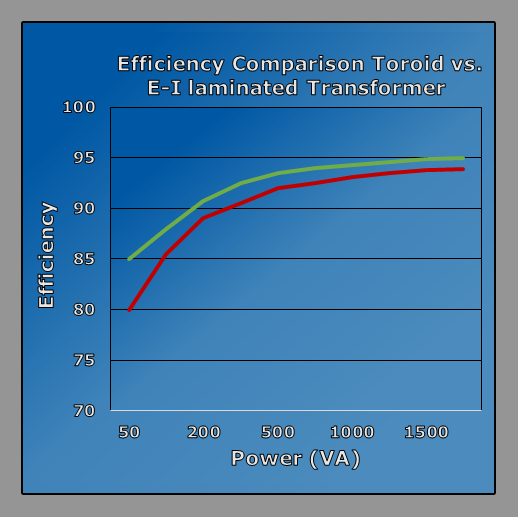
The combination of very low core losses (1/2 watt per pound), a lower mean length per turn, and fewer turns yield lower I2R losses. This unique construction allows toroid power transformers to be typically between 15% and 30% more efficient than E-I laminated transformers. As a rule, the larger the transformer the more efficient a toroidal transformer becomes.
LOWER OPERATING TEMPERATURE
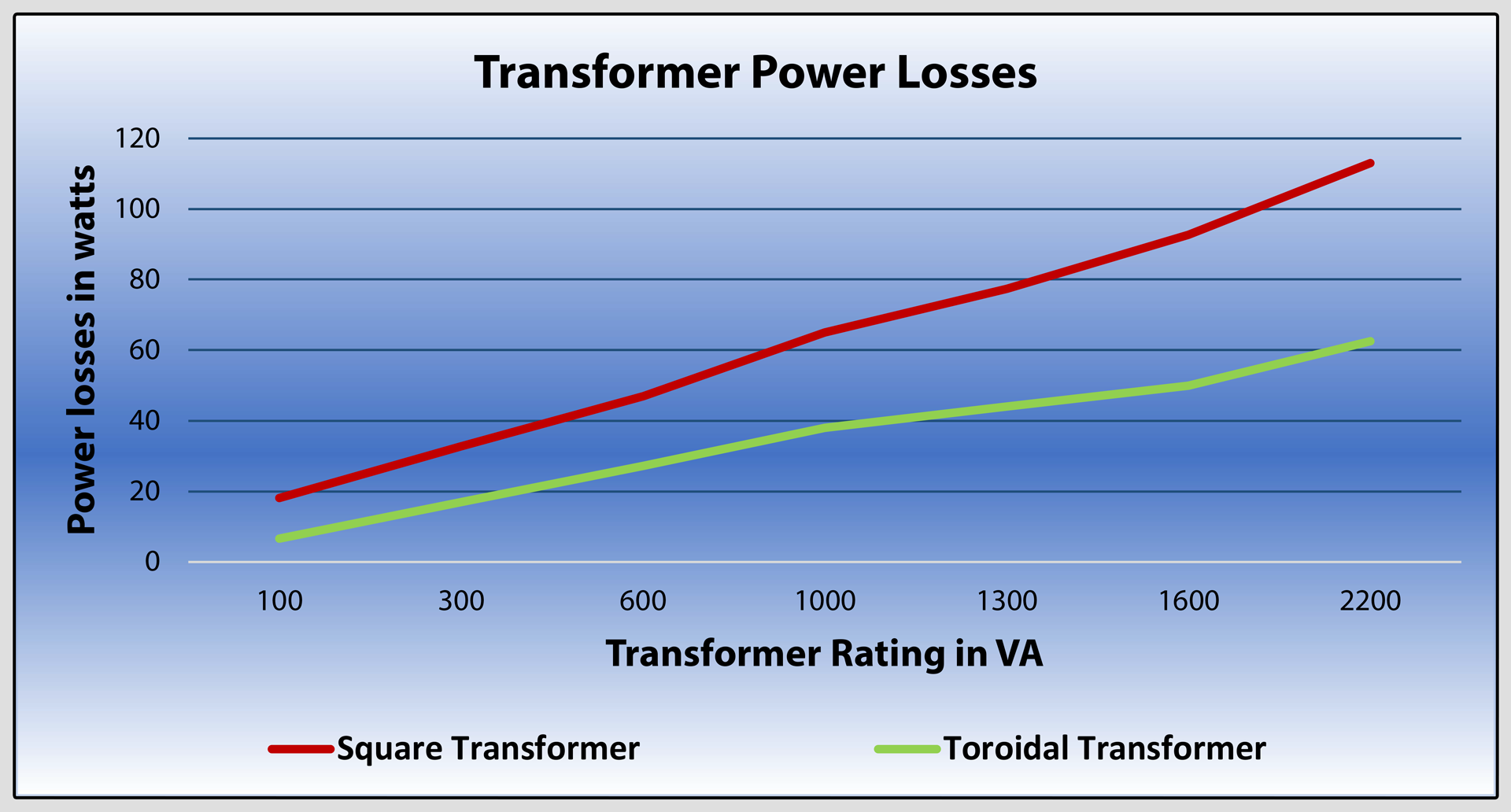
Since most of the losses in a toroid transformer are in the copper wire, the toroid cools off quicker than the conventional E-I transformer type with more iron. At half the load, the toroidal transformer's temperature rise is only about 30% of what it is at full load.
FLEXIBLE DIMENSIONS
Power toroids and power chokes are not constrained to specific lamination sizes. Since the height and diameter of toroids may be carefully varied, it allows flexibility to accommodate specific height and width design requirements.
RADIATE LOWER MAGNETIC FIELDS
Toroid transformers, including toroidal medical isolation transformers, are made from one solid piece of material focusing the field within the core. In addition, the primaries and secondaries are wound uniformly around the entire core. This results in very low radiated magnetic fields. The toroidal transformer is perfect for applications with circuitry, which is highly sensitive to stray magnetic fields. In certain cases, the single bolt mounting allows the toroid to be rotated in place, to yield the best possible results without any additional tooling or sheet metal work. This can be specifically important in medical equipment having especially sensitive electronics; a toroidal medical isolation transformer typically can be placed in closer proximity to these electronics without additional shielding.
SMALL SIZE
Toroidal power transformers have lower core loss, operate at a higher flux density, and allow the conductive windings to be in intimate contact with the core. This enhances current flow at all points in the core yielding a transformer, which is smaller than its E-I transformer counterpart. Electrical and mechanical designers appreciate a toroid’s compact dimensions especially where low height is a consideration.
|